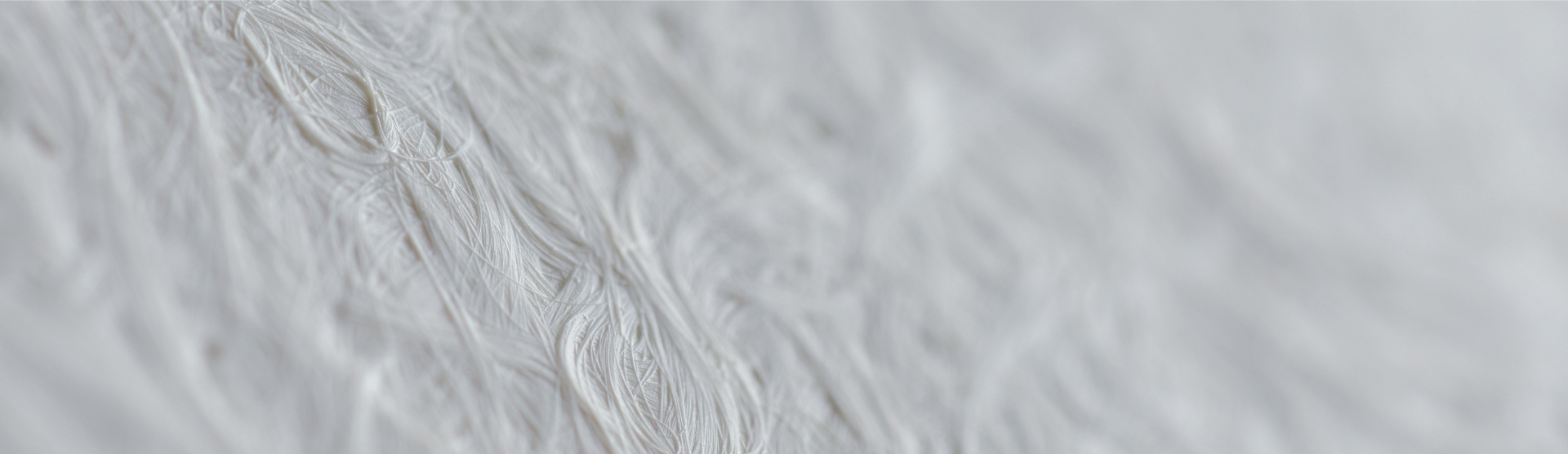
Sheet Moulding Compound (SMC)
BFG Africa uses a variety of methods to produce FRP parts. Our experienced engineers will select the best method for your project based on factors such as production volume, parts dimensions, budget, and other requirements.
Our extensive experience with press moulding enables us to produce innovative and cost-effective parts for our OEM customers.
The process is best suited for large structurally reinforced parts requiring two-sided finish. It is best for moderate to high production quantities of between 5,000 and 10,000 parts per year
Process
Sheet moulding compound (SMC) is both a process and reinforced composite material. The composite is a “ready to mould” glass or carbon fiber reinforced polyester material primarily used in compression moulding. The SMC sheets are manufactured in a continuous in-line process by dispersing long strands of chopped glass fibers or carbon fibers on a bath of polyester resin, vinyl ester resin or epoxy resin. It is a flexible, leather-like sheet that is easily cut, weighed and placed in the mould for curing to the desired part configuration.
SMC materials are thermosets and contain glass or carbon reinforcement levels between 10 and 60 percent. The longer fibers in SMC result in better strength properties than standard bulk moulding compound (BMC) products. Standard SMC contains up to 35 percent of randomly oriented fibers by weight. Because there is no mixing or extruding involved in preparing sheet moulding compound, the fibers remain undamaged and at their original lengths. This plus the higher fiber loading provides very good mechanical properties in compression-molded SMC parts, especially those having relatively thin cross sections.
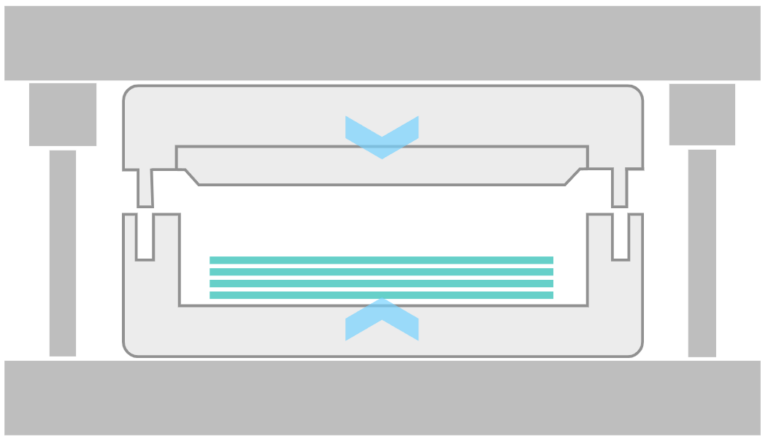
Material options
RESINS
Vinyl Ester
Epoxy Resin
FIBRES
Any
CORES
Foam
Advantages
- SMC delivers high surface quality with excellent detail, including ribs, bosses, inserts
- SMC is used for larger parts where higher mechanical strength is needed
- SMC parts display excellent temperature and fire resistance
- Piece parts are cost effective solutions for structural and non-structural applications
- SMC Structures have long life and require little maintenance.
Limitations
- Because SMC flows in the mould, fibre orientation and properties can vary throughout a part, particularly in deep-drawn shapes
Applications
- Demanding electrical applications
- Corrosion resistant needs
- Structural components at low cost, automotive, and transit
- Class A body panels
- business equipment cabinets
- personal watercraft
- structural components
General Design Guidelines
Minimum Radius | 1 mm (0.0625 in) |
Minimum Draft | 4 degrees |
Minimum Thickness | 3 mm (0.125 in) |
Maximum Thickness | 13 mm (0.500 in) |
Typical Reinforcement Loading | 10 – 60 % |
Density (GP resin) | 1938 kg/m3 (.070 lb./in3) |
Die Lock (Reverse Draft) | Yes |